Support
Equipment Selection Assistance
Please tell us the product you are making or would like to make and we will work to determine the best machine for your application.
Technical Support
Available for our machinery customers for the life of our machines, technical support includes troubleshooting equipment or machine specific process problems.
Mold Design Assistance
CCMCO provides mold design drawings with our machine packages. For customers who use another supplier's machine we can quote mold design services for your specific machine and casting.
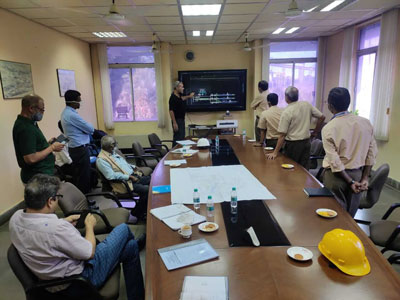
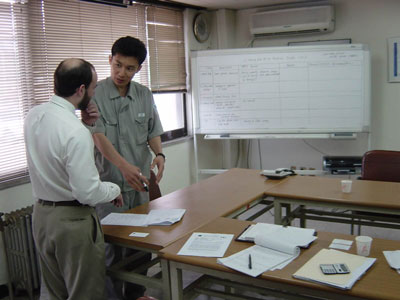
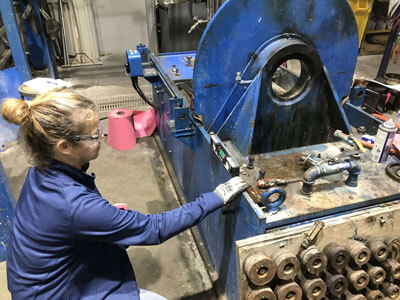
On Site Services
Operator Training
Designed specifically for the individual needs of our customers, Operator training is offered at the customer's site. Whatever your knowledge level of centrifugal casting, we can develop a program especially for you.
Machine Maintenance Service-One Time
CCMCO can come to your site to handle a one-time machine maintenance issue. Our team is versed in changing out bearings and rebuilding spinners among many other things. While your team is busy producing product we can supervise or completely handle machinery maintenance projects.
Process Consultation
We work with our customers, both those who have our machines and those who do not to improve their casting process. As we tell our customers, our machines do not care what we pour into them, it is the process that makes the difference!
We can offer a no cost 30 minute consulting session during which time we can determine the best way forward. CCMCO can either come to your site, or offer assistance using video conference and email or chat. We want our customers to be successful in their casting production!
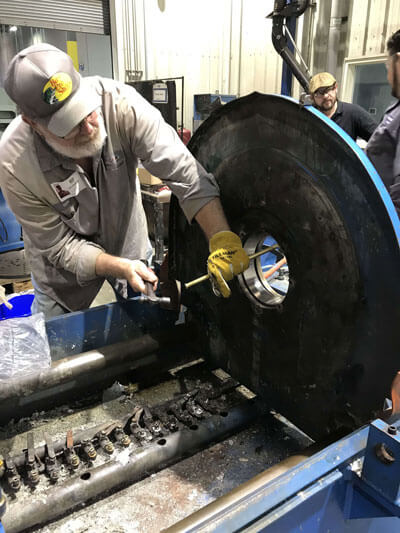
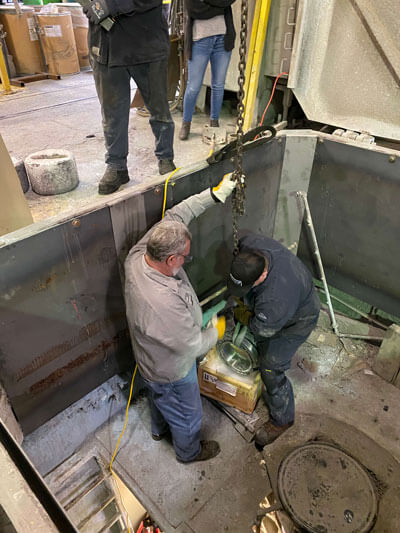
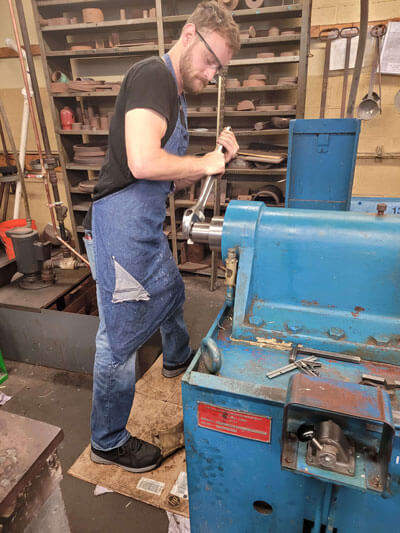
Annual Maintenance
CCMCO offers Annual Maintenance contracts to our customers. Some of the items we might accomplish during our time on site are:
Vertical Machines
- We could be present for changing bearings and seals in the spinner assembly.
- Train operators on best practices for performing this operation.
- Check and maintain the oil mist system.
- Check for clogged or worn burner or water nozzles. Replace as needed.
- Check belts for wear.
- Conduct a thermal study to check for hot spots. This can indicate loose lugs, or a component that is coming to the end of its life.
Horizontal Machines
- Be present for changing bearings and seals in the spinner assembly.
- Train operators on best practices for performing this operation.
- Help with grease lubrication if needed.
- Check for clogged or worn nozzles. Replace as needed.
- Check belts for wear.
- Conduct a thermal study to check for hot spots.
- Examine the Rolance system. Replace the Spray nozzle, should it be required.
Other items that customers might use CCMCO for while we are on site:
- Supporting Client in developing Safety and Operating procedures for training machine Operators.
- Advising on new or existing mold designs.
- Providing consultation on current centrifugal foundry set up, operation and plans for future capacity expansion.
- Helping to analyze parts currently sand casted for consideration for centrifugal casting.
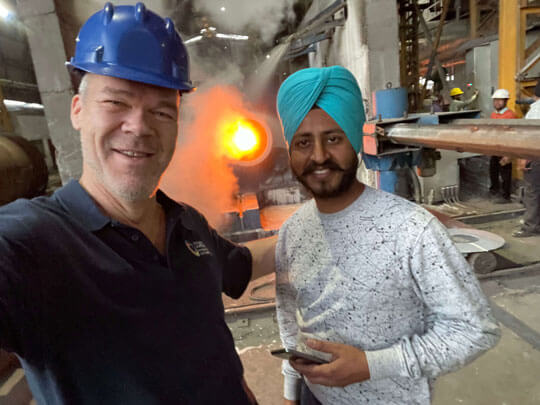
Foundry Audit and Dream Foundry Development
The CCMCO team spends a lot of time in foundries. When we visit we often ask our hosts, what would your dream foundry look like. This sparks many conversations that usually result in lists being made.
- Short-term
- Mid-term
- Long-term
Or
- Low cost
- Medium cost
- Ultimate foundry
We believe that you don't need to dig up the foundation to see improvement in the foundry. Small changes can often be made to a customer's existing foundry that can make a big impact. For example, we can change the spray tips on existing lances to try to minimize the number of coating application passes. With minimal investment you can decrease cycle time and increase casting quality.
Talk to us about your dream foundry today and see what happens.
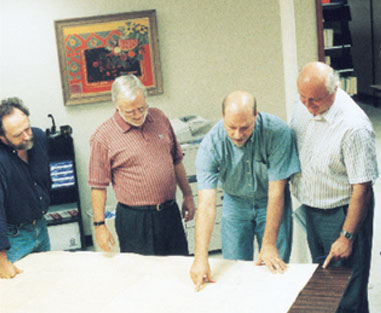
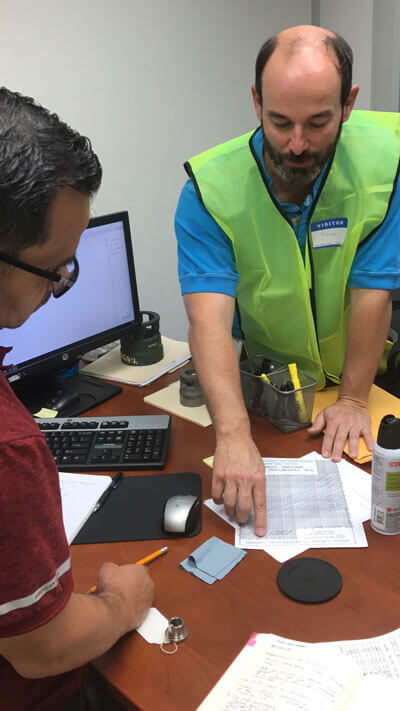
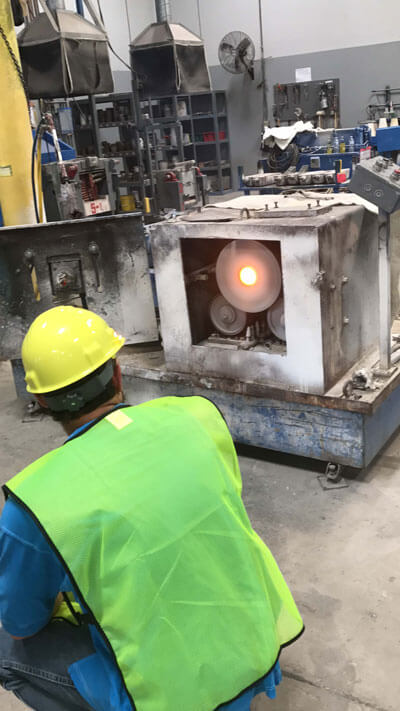
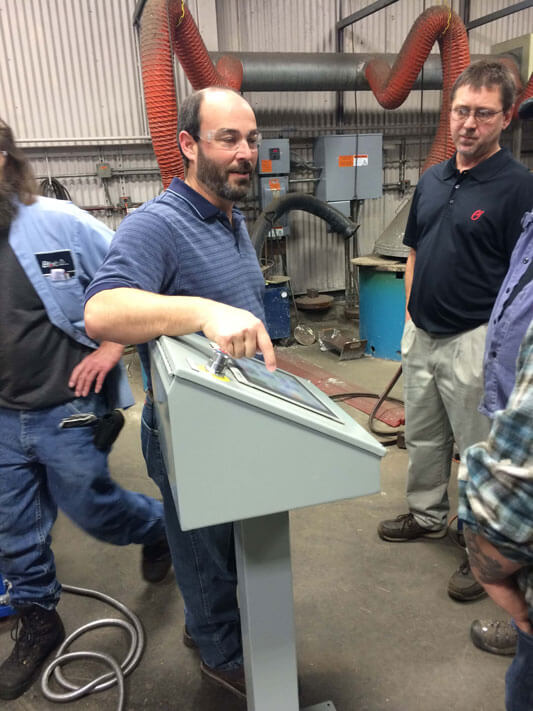